AGV车架有限元分析及结构优化
胡忠义,黄雪涛*,许永超,刘子豪,王宪成
山东交通学院汽车工程学院,山东 济南 250357
摘要:为解决自动导向运输车(automated guided vehicle,AGV)车架在使用中出现裂纹的问题,基于Solidwork建立车架有限元模型,采用Hypermesh对车架弯曲工况、扭转工况、转弯工况、制动工况进行静力学分析,确定危险工况及应力集中部位;增加车架中间纵梁、第3横梁、第6横梁的槽钢厚度,在第3横梁、第6横梁与纵梁交叉处设置加强筋,并对优化后车架的扭转工况、转弯工况进行静力学分析和模态分析。结果表明:优化后车架的扭转工况和转弯工况的最大应力均降低,安全因数符合设计要求;优化后车架不再发生低频共振,解决车架裂纹故障。
关键词:AGV车架;有限元分析;静力学分析;模态分析
Finite element analysis of AGV frame and its optimization
HU Zhongyi, HUANG Xuetao*, XU Yongchao, LIU Zihao, WANG Xiancheng
Automotive Engineering College,Shandong Jiaotong University, Jinan 250357,China
Abstract:In order to solve the problem of cracks in the frame of an automated guided vehicle (AGV) during use, a finite element model of the frame is established based on Solidwork. Hypermesh is used to conduct static analysis of the bending, torsion, turning, and braking conditions of the frame, identifying dangerous conditions and stress concentration areas. The thickness of the channel steel in the middle longitudinal beam, 3rd crossbeam, and 6th crossbeam of the frame is increased, and the thickness of the channel steel in the 3rd crossbeam install reinforcing ribs at the intersection of the 6th crossbeam and longitudinal beam, and conduct static and modal analysis on the optimized torsion and turning conditions of the frame. The results show that the maximum stress in the torsion and turning conditions of the optimized frame has been reduced, and the safety factor meets the design requirements; After optimization, the frame will not experience low-frequency resonance, solving the problem of frame cracks.
Keywords:AGV frame; finite element analysis; static analysis; modal analysis
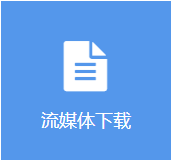